Protection of the building structure
Core drillings don’t leave any subsequent damage on
sensitive parts of the basic structure of a building
since they operate vibration-free.
Environmentally friendly and clean
With core drilling, concrete compounds can be
broken down into any desired size. Therefore they
can be easily disposed of and dumps or waste
disposal sites are no longer needed. Further, core
drilling uses water cooling and is relatively fast
executed, noise pollution and dust formation are
reduced to a minimum.
Ready anytime and anywhere
In particular, the wire saw is among the diamond
cutting techniques for hard to reach objects, intricate
cuts and in sensitive environments. Even core drilling
or sawing under water are no problem.
We use our own fleet of screed pumps to site mix the screed. With our years of experience we
have the knowledge to know the exact quantity of materials to use. Using our screed pumps to
site mix the screed gives greater flexibility, ensuring that we have control over standards of
materials used and is more economical. We can install screeds up to 2500m² per day.
Most Common Types of Screed
A Screed or sometimes called Screeding
is simply a type of concrete used to form
a level surface either to receive floor
finishes (such as floor tiles or carpeting),
to encase underfloor heating pipes or to
be left as the wearing surface. It is laid
either on top of the excisting concrete
base, a damp proof membrane (DPM) or
insulation.
Screeding is the process of cutting off
excess wet concrete to bring the top
surface of a slab to the proper grade and
smoothness.
Traditional Screed / Sand Screed
Traditional Screed is also known as Sand
cement screed and is used for many
applications. They are designed to provide a
smooth, flat, level surface, suitable to receive
the floor coverings.
Sand cement screed can be batched on site
using modern screed pumps.
Liquid Screed / Flow Screed
Liquid screed, also known as flow screed is a
screed in liquid form and can be pumped onto
both ground and upper floors.
The benefits of liquid screed are enormous.
Large spaces can be covered in a short period
of time, reducing man hours. Shallower floor
depths can be achieved and set to laser
accuracy. Liquid screed can be bonded and
un-bonded, like traditional screeds.
Other types of screed
Other types of screed inlcude Fibre screed,
fast drying screed, polymer screed
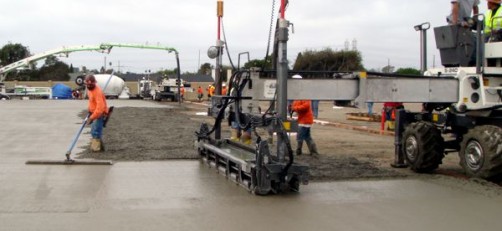
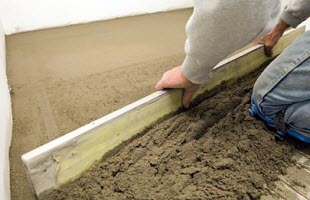
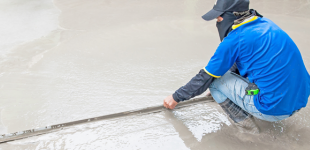
Screed mixing
The screed mix generally consists of sharp sand, cement
and water and standard ration is a 1:4 mix design. It needs to
be mixed using a forced action that is provided by a screed
pump which ensure that it is accurately batched and fresh.
Pumps also transport the mix to the working area.
Process
We survey the space with a laser level, take measurements
from the datum and transferring this across the space. We
also ensure that this level is applied to the middle of the floor
and the perimeters.
When laying the mix, we manually compact it to expel any air,
which helps prevents voids or hollows and further
strengthens it. This is also not a common practice in the
industry but as we take such pride in the quality of our work, it
is a method that we train our screeders to do.
Our screed is laid to the highest standard of surface
regularity. This means a spot on surface for your floor
finishes which is the whole point of having a screed laid.
Expertise
We can provide you with the correct technical knowledge, experience mathced with skills and
equipment to ensure the perfect result for your project. We can work with a wide range of
different screeds so we can provide you with the best possible result at the best price.
See here for more information on screed and about
the floor screeding process: