Concrete is the most common base. The designer must establish the surface characteristics of
the slab and the normal thickness being allowed for the screed early in the design process. The
thickness will have a large influence on the make-up and method of laying, as well as the nature of
the bond. Screeds can be laid on timber but it must be stable and a good-quality damp-proof
course must be used.
Screed can achieve a high-quality finish with less than 3mm deviation over any 3m. The finish
material defines the quality needed. For thinner materials such as a vinyl less than 2mm thick, an
even and blemish-free finish is needed.
Screed is usually a cementious material made from a 1:3 to 1:5 ration of cement to sand. A simple
cement and sand mix will be fine for a simple application but more sophisticated mixes are suitable for
a wider range of apllications. There are screeds that can be pumped in to place and are used to achieve
very level finishes thus allowing flexibility in laying.
Pumping the Screed
The sand, cement and water are mixed in the screed
pump machine and is then pumped via hoses to the
desired concrete area.
Spreading the Screed
The pumped screed is poured over the concrete
construction and divided with a floor wiper. In this way
the top-layer will be reinforced. The “semi-dry” screed
can be compacted and finished by simple hand methods
using a steel float or a screed board to give it a uniform
cover.
Screeding
The actual screeding process involves dragging a screed
board over the partially-compacted course material and
scraping-off the top layer to create a smooth, profiled
laying surface. After the screed has been spread,
compacted and screeded to level, it will be bull floated
or power trowelled.
Compacting & Finishing
Hand compaction of screeds may be carried out using a
screed board with a vertical chopping motion. The
compaction will be made much easier and more
efficient with the use of a hand rammer, a roller, or a
mechanical plate vibrator. A wooden or steal float may
be used to finish the screed. Steel trowels should not
be used until all bleed water has evaporated from the
surface.
Unbounded screeds ranging from 60 to 75mm thick can be laid at any time after the slab has been
constructed. They will usually have a damp-proof course separating them from the sub-floor. They
must be allowed to dry slowly, however, as fast drying will make them cure like a curly sandwich. If the
floor loading requires it, the screed may need reinforcement. This can be achieved either by the
addition of plastic particles to the mix or the use of one layer of fine reinforcement.
Services
Thicker screeds can be accommodate services,
but it is rarely a good idea to place these directly
in the screed. It is a better practice to feed pipes
and cables through a conduit, particularly heating
pipes, as these expand and contract. Typically,
the heating elements in underfloor heating
systems are surrounded by a specially designed
screed. This includes plastic reinforced pipes that
can flex with temperature and a screed
compound that will not crack even if relatively
thin.
Movement Joints
Movement joints must be considered as these
restrict the stress that can build up with the
material and control cracking. Ensure that any
building movement joints are mirrored in the
screed, too. No large areas or significant changes
in finish should be designed without a movement
joint so you will need to seek expert advice.
Shape should also be considered. Keep each area
of screed as rectilinear as possible and
incorporate movement joints at all changes of
level, structural elements and fixed points.
Curing
Screeds are cured as soon as possible after laying
by covering them with polythene sheeting. This
ensures that all the water remains in the mix
allowing the full strength of the screed to
develop. After curing, screeds should be allowed
to dry out naturally. Accelerated dying will
increase the probability of dying shrinkage cracks.
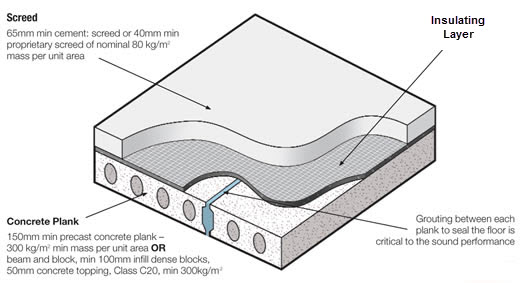
Cement
Cement is a binder that sets and hardens independently, and
can bind other materials together.
Sand
Clean and sharp sand is used. An excessively fine or dirty sand
will result in a screed of insufficient strength and durability with
increased drying shrinkage and curling.
The Mix
A sand:cement mix of 4:1 batched by weight is generally used.
For screeds of over 50 mm thickness, a concrete screed may be
used (10 mm maximum aggregate size). Such a screed would be
laid as would concrete, i.e. with a higher workability than a
sand/cement screed.
Screeds can be bonded to the sub-floor or unbonded.
Bonded screeds are laid directly to the new sub-floor or
chemical agent is applied before laying to ensure a good
bond. This ensures the screed acts as one with the slap
below. However, the laying process must be
undertaken carefully to ensure de-bonding does not
occur this will make the screed unstable and it will fail.
Usually, thinner screeds are bonded. An unbounded
screed of less than 50mm must be designed using a
specific mix to ensure it is strong enough.
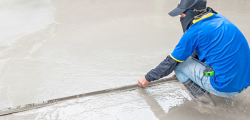
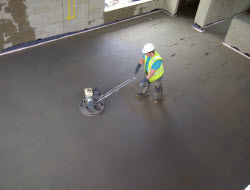
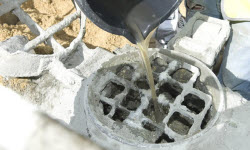
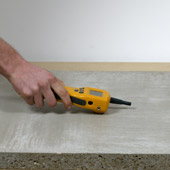
Screed thickness & moisture control
The moisture in a new screed needs time to evaporate.
Especially screeds more than 10mm thick contain large
quantities of water that needs to dry out. Otherwise
they can cause significant disruption late in the build
process. Moisture content is important, as most floor
finishes and adhesives are sensitive to it. They are also
sensitive to the build-up of water vapor if it is sealed in
to the screed. This has resulted in the development of
screed compounds that chemically control the water
used. Optimum screed thickness is from 30 to 70 mm as
there are a large number of sophisticated and versatile
compounds available for this range.
See here for our screed pumps and other
equipment used for the screeding process.
You can check out as well as all our other
equipment and machines for our other services.
A screed is usally a mix of cement, water and
sand laid over a concrete base to provide a
surface close to a specified level. To achieve a
good-quality solid flooring, the use of screed is
needed. In many cases, it is not desirable or
practical to apply the floor finish directly to the
structure. So a screed is applied to create a
smooth, level surface. Screeds can also be used
to enclose heating elements or as a path to route
services.
Three basic criteria are at the heart of good
screed design: strength, bonding and moisture
control. With floor screeds, the standard of
materials and workmanship will greatly affect the
quality of the final material.